At Sioen CSR Initiatives: search for alternative sources of energy
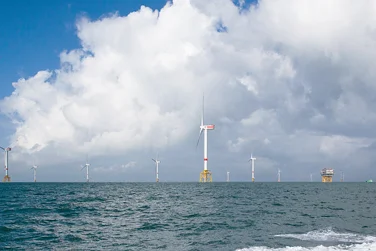
Gas and electricity consumption has been greatly reduced over the past years with the optimisation of machinery at the direct coating plants in Ardooie, Belgium. At all coating plants, emissions are treated by thermal destruction with energy recovery at on-site high performance incinerators.
Sioen has installed solar panels wherever feasible at its Belgian and French sites. Approximately 35000 m² of solar panels cover around 3.48 % of total electricity needs. , they again installed additional, brand new solar panel parks on our production units in Mouscron (Belgium), on a surface of approximately 2 900 m². The Group has signed an energy-saving ‘Audit Covenant’ with the Flemish government and very similar ‘accords de branche’ (industry agreements) with the Walloon government. , external energy audits have been a primary force in driving its energy-saving plan.
Packaging materials: Cardboard, PE foil and PMD is gathered for recycling. Sioen is a member of Val-I-Pack which promotes the management of recycling of industrial packaging waste.
The recycling unit at Sioen Fibres enables us to recycle all polyester production waste, such as hard lumps and yarns from the spinning-mill, edges and fabrics from the weaving mills and uncoated fabric leftovers from the coating division. As a result the spinning-weaving-coating process is virtually waste-free, resulting in a cleaner environment and a rational answer to ever-increasing raw material prices and availability issues. In the calendaring process, all production waste is being reused as raw material in the production process (approximately 757 tons a year).
Recycled packaging material: cardboard: 129 tons, wood: 383 tons, metal: 225 tons and plastic: 120 tons.
Impact: In all our plants in Belgium and France we use mains water, ground water and rainwater. 1. Cooling water: This is needed for the coating units and in the production of yarns, pastes and inks. For this we use ground and rain water, always in closed circuit. 2. Nebuliser: In each of our weaving plants, water is sprayed over the looms to ensure constant humidity. For this we use ground water. 3. Cleaning water: To clean barrels at our online coating and chemicals facilities. For this we use 3 011 tons of water. 4. Sanitary water: For this we use rainwater, topped up with mains water as necessary. 5. Extinguishing water: Rainwater provides the extinguishing water reserve in all our production plants.
Initiatives: With the exception of sanitary water, we aim for zero discharge status. Our online coating plant at Ardooie and our chemicals production plant at Bornem have already achieved this.
Impact: The Coating Division is the main user of electricity in the Group worldwide, accounting for 95% of consumption, to power the machinery at the spinning mill and the online coating plant., the group used 78 280 MWh of electricity.
Initiatives: Sioen has installed solar panels wherever feasible at its Belgian and French sites. Approximately 35000 m² of solar panels cover around 3.48 % of total electricity needs., we again installed additional, brand new solar panel parks on our production units in Mouscron (Belgium), on a surface of approximately 2 900 m². The Group has signed an energy-saving ‘Audit Covenant’ with the Flemish government and very similar ‘accords de branche’ (industry agreements) with the Walloon government. Since 2007, external energy audits have been a primary force in driving its energy-saving plan.
Impact: Packaging materials: in an outward direction, Sioen uses only recyclable and/or reusable packaging material. In an inward direction, we press our suppliers to minimise the amount of packaging material.
Initiatives: Packaging materials: Cardboard, PE foil and PMD is gathered for recycling. Sioen is a member of Val-I-Pack which promotes the management of recycling of industrial packaging waste.
Impact: Hazardous waste: essentially high-caloric solvent residues from the coating processes. we carried some 578 tons of hazardous waste to authorised processors.
Initiatives: Hazardous waste: We continuously invest in distillation installations, to reduce this amount.
Impact: White spirit & DMF: we use approximately 947 tons of white spirit every year in our production process, primarily as a cleaning agent for paste barrels. DMF (dimethylformamide) is the main solvent used in the transfer coating process (around 806 tons a year).
Initiatives: After use this solvent is distilled and reused with the sediment (a PVC residue), and sold as a raw material for producing floor tiles. All DMF is distilled and reused in the production process.